Several important factors must be considered when planning to build an industrial or factory shed. The right choices will result in a shed that fits your needs, works for your industrial application, stands the test of time, and delivers an optimum return on your investment
Purpose And Functionality
Before starting construction, you must know the intended use of the industrial shed; storage, manufacturing, warehousing etc. to design the layout, size and specific features accordingly.
Size
Industrial shed comes in several sizes. Depending on the size you need to consider the volume of work produced within the shed, a number of workers will be in given time, equipment, material, tools etc. Based on this you can decide how much space you will need.
Material
Choosing the right material for an industrial shed is very important. Fibre cement corrugated roofing sheet is best for industrial sheds because of its: –
- Durability: Fibre Cement roofs are durable and robust, providing excellent resistance against extreme weather conditions, including heavy rain, wind, UV rays, and temperature fluctuations. They withstand harsh environmental conditions and have a longer lifespan than other roofing materials.
- Fire Resistance: Fibre Cement roofs are extremely fire-resistant, making them a safe choice for industrial structures where fire safety is crucial. They offer a higher level of protection against fire hazards compared to materials like wood or asphalt shingles.
- Low Maintenance: Once installed, fibre cement roof requires minimal maintenance. They are resistant to rot, decay, and insect damage, reducing the need for frequent repairs or replacements.
- Insulation and Energy Efficiency: Fibre cement roofs offer good thermal insulation, helping regulate interior temperatures and potentially reducing energy consumption for heating or cooling. This feature can contribute to energy efficiency in industrial buildings
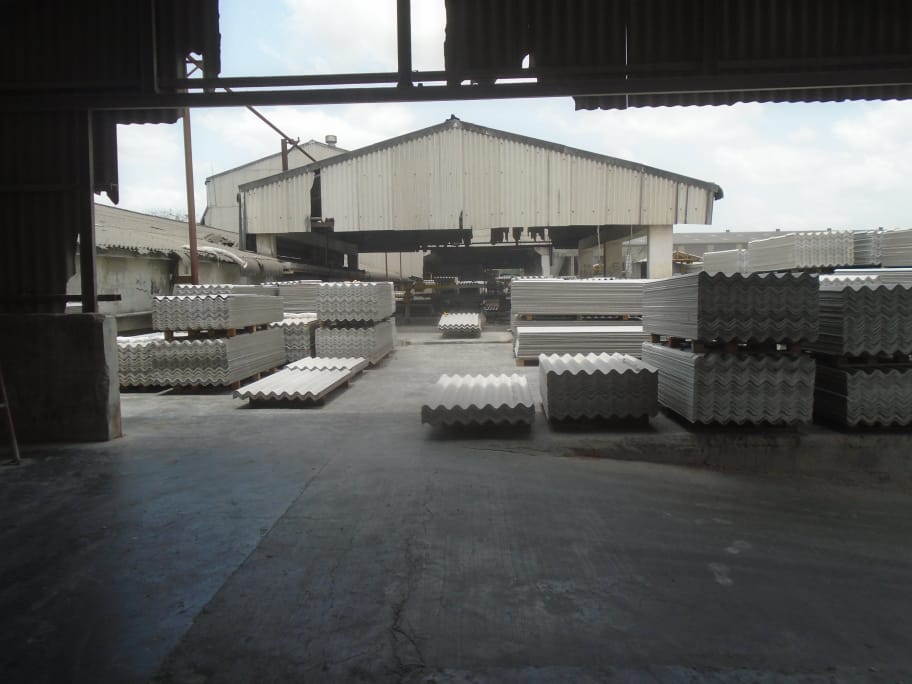
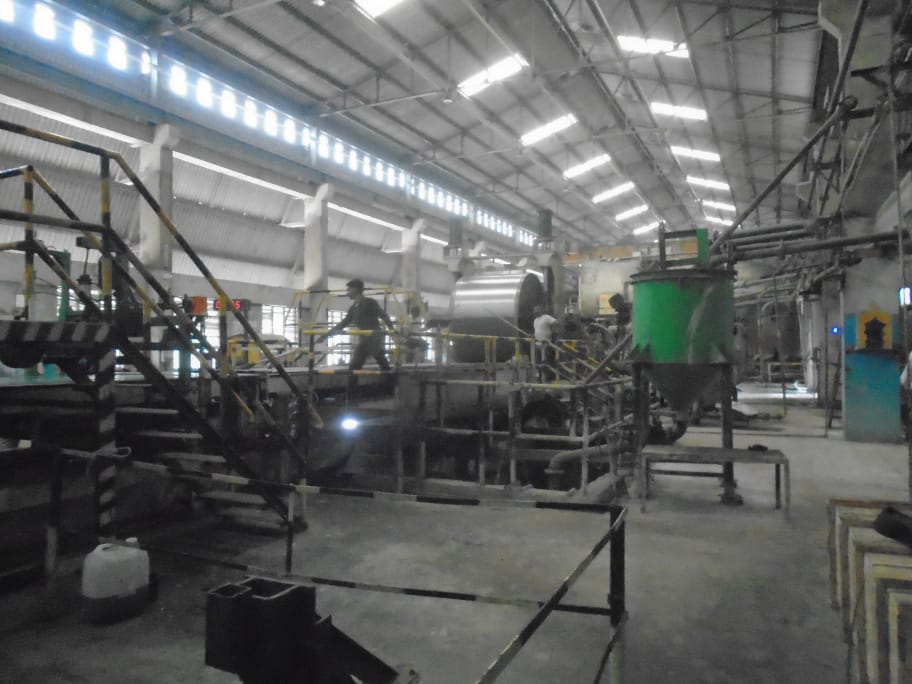
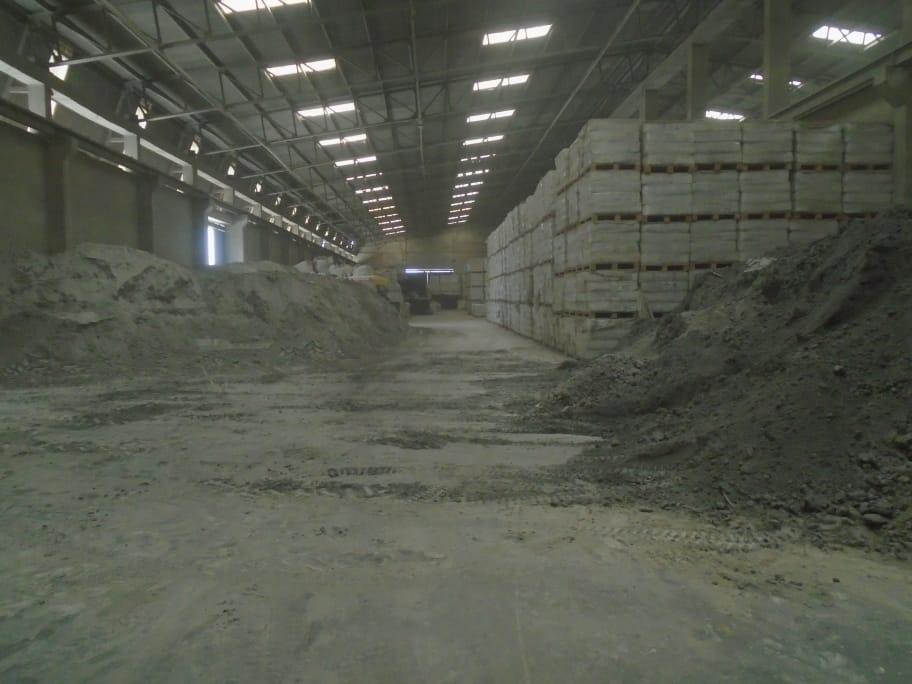
The cost of the building shed
- Industrial shed needs significant investment. You must consider how much you’re willing to spend on materials and the labor cost associated with erecting the shed.
- Evaluate long-term operational costs, including maintenance and utilities, to ensure financial viability.
Design of the building shed
- Engage with experienced engineers, architects or construction professionals to design, plan and execute the project.
- Ensure flexibility / future expansion in design layout.
- Consider the access to water, electricity, drainage, HVAC system and other essentials required for design.
Safety and Security Measures
- Incorporate safety features such as fire suppression systems, emergency exits, proper ventilation and lighting to ensure a safe work environment.Build fencing and install surveillance systems for inventory or asset protection.
Mezzanine Floor
- It is an intermediate floor or platform constructed inside the industrial shed without extending the length or width of the building to provide additional floor space within the existing structure.
- Cemply 18 sheet provides you a light weight strong floors. Above this sheet, you can lay tiles, lightweight concrete or anything that you want to make your floor beautiful
- The advantages of Cemply 18 are thermal resistance, acoustic resistance, water resistance, fire resistance, lightweight, easily mountable and easily relocatable floors